Lexus Carbon-Fiber Use Leads to Less-Expensive Application
Using thermoplastic resins for the LFA’s body, instead of thermoset resins, likely will lead to greater use of carbon fiber in mass-produced cars, says Nobuya Kawamura, project manager.
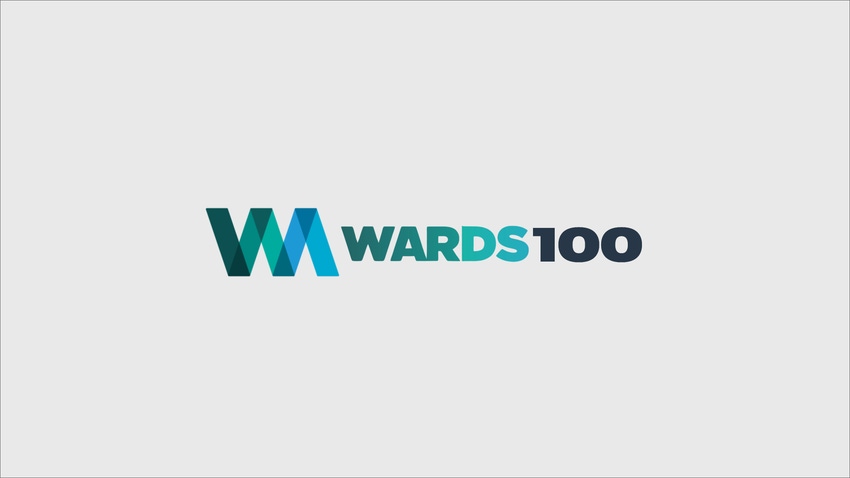
PARIS – Using carbon fiber for the body of the upcoming Lexus LFA supercar helped Toyota Motor Corp. identify automation techniques that will lower the cost of using the material in higher-volume vehicles.
Specifically, using thermoplastic resins, instead of thermoset resins, likely will lead to greater use of carbon fiber (CF) in mass-produced cars, says Nobuya Kawamura, project manager for the Lexus LFA at Toyota’s vehicle material engineering division.
But even for a car that will sell for about $500,000, cost was an issue during development.
“We struggled in the cost area (on) how to reduce the labor cost,” Kawamura says in a presentation at the recent JEC Composite exposition here.
The LFA project began by using CF-fiber textile impregnated with resin, ready to put into a high-pressure mold. Later, says Kawamura, engineers began developing parts using a resin transfer-molding process that is more automated and less expensive.
By the time they were satisfied the car could go into production in December 2010, the engineers had improved a variety of techniques to use the lightweight, strong material.
“It’s a never-ending process,” Kawamura says.
The curb weight of the super sports car, first introduced as a concept at the North American International Auto Show in Detroit in 2005, is 3,263 lbs. (1,480 kg), of which 35% is aluminum castings and extrusions and 65% is CF-reinforced plastic.
“With aluminum, the car body would be too heavy,” Kawamura says.
The final 552-hp Lexus LFA has a weight-to-power ratio of 5.8 lbs. (2.7 kg) per horsepower, slightly more than the 570-hp Lamborghini Gallardo LP 570-4 Superleggera at 5.2 lbs. (2.4 kg) per horsepower.
Lexus LFA weighs about 3,263 lbs., of which 35% is aluminum castings and extrusions and 65% is carbon-fiber-reinforced plastic.
Toyota engineers have taken different approaches for different parts. Among them:
The CF for the hollow A-pillar is woven by a 3-dimensional machine to achieve different profiles, depending on the needs of the body structure at different points.
The front-end crash-absorbing structure behind the bumper is 3D woven carbon fiber.
The rear parcel shelf and some roof pieces use a carbon-filled sheet-molding compound, which is less rigid than steel but still twice as strong.
The floor and center tunnel are constructed with Resin Transfer Molding. “We started with a pre-preg approach and ended with a 1-shot RTM at 180º C (356° F),” Kawamua says.
The tunnel, which carries the drive shaft and two exhaust pipes, has a double wall area around the exhaust pipes and is heavily insulated to control heat.
Pre-preg was used for the firewall and rocker panels. The firewall is a sandwich around a moldable polyurethane foam. Rocker panels use a thermoplastic epoxy-based resin. Inside, a corrugated CF structure encapsulated in rigid polyurethane foam provides side-impact strength.
For the pre-preg material, Toyota developed a Non-Crimp-Fabric, rather than a woven fabric. Kawamura says woven CF results in voids, where threads cross that are difficult to evacuate when filling with resin.
:By laying threads over one another in two directions and then stitching them together, the voids are easier to evacuate. The easy evacuation, and a resin with a viscosity tuned for the project, means the pre-preg material can be processed without using a sealed autoclave mold. Such molds have a slower cycle time.
By laying threads over one another in two directions and then stitching them together, the voids are easier to evacuate. The easy evacuation, and a resin with a viscosity tuned for the project, means the pre-preg material can be processed without using a sealed autoclave mold. Such molds have a slower cycle time.
Toyota’s ambition to build a supercar reportedly began in 2000, and Kawamura says early versions used more aluminum. But then the auto maker decided to make only 500 cars, instead of 2,500.
In 2006, the engineering team chose CF for the body, with a cast aluminum subframe in front attached to an extruded aluminum crash-absorption device, and an aluminum subframe in back essentially to make crash repairs easier.
Engineers tore down a Porsche Carrera GT and Mercedes-Benz McLaren SLR for benchmarking.
The Lexus packaging uses a front mid-engine and a short overhang, with 48% of the weight on the front axle. The LFA is 177 ins. (450 cm) long on a 102.6-in. (261-cm) wheelbase. It is 48 ins. (122 cm) high.
About the Author(s)
You May Also Like