IKEA’s Flat-Pack Model Comes to Car Building
How alternative vehicle production methods are disrupting traditional thinking.
November 7, 2023
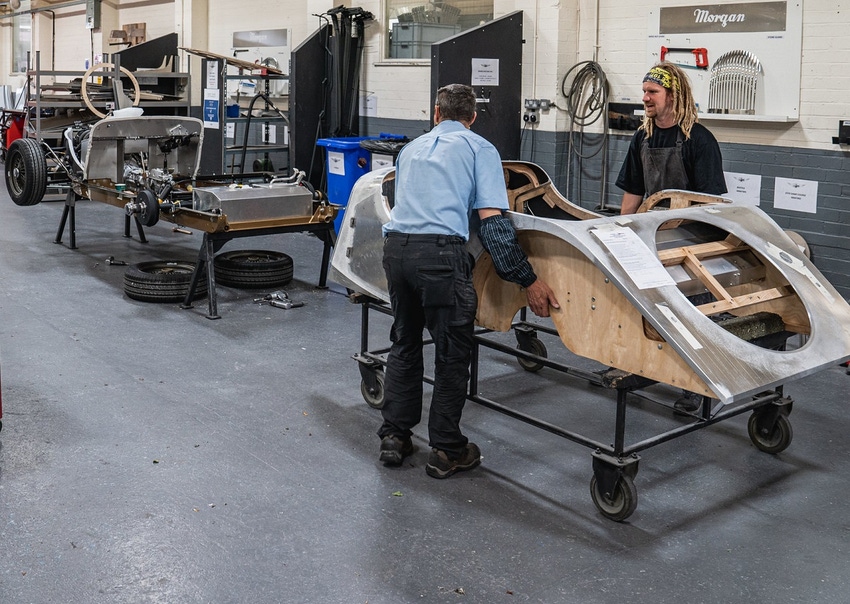
Is there an equivalent to IKEA in today’s auto industry? An early-stage company in IKEA’s native country of Sweden called Luvly certainly qualifies.
Its inaugural model is the Luvly O, a small battery-electric 2-seater characterized as a “light urban vehicle” (LUV) that’s currently in pre-order. It’s hardly the first modest-sized BEV on the market, but what sets it apart is the way it’s produced. The cars ship in a flat-pack box to third-party microfactories where they are assembled into their final road-worthy form.
As with nearly every other aspect of vehicle production, ambitious young automakers are aiming to disrupt traditional models. Flat-pack is one of several innovative methods coming onstream; others include gigacasting (also known as megacasting) and 3D printing.
For Luvly, the flat-pack method aligns with its stated goal of making car production cleaner and greener. There are other advantages, too. According to the company’s founder and CEO Håkan Lutz, flat-pack “Massively reduces emissions. Compared with electric cars, energy consumption from LUV production, shipping and distribution is up to 80% lower and this also means that mass production can be made exceptionally cost-effective and fast.”
Interestingly, the Luvly boss doesn’t necessarily see the company’s move as disruptive. “The flat-pack model is not inherently contradictory to in-house production but, rather, is a more efficient means of distribution that can be enabled by technology; in-house production tends to be a less efficient impact model than licensing,” Lutz says.
Of course, alt-production methods don’t necessarily have to be outsourced to partner businesses. Nor must they be adopted only by would-be disruptors. Some established automakers are happy to continue maintaining their proprietary lines, especially given that building them is a long and expensive trek.
One of the more prominent examples of this is Tesla’s much talked about “gigapress”. This is essentially an up-to-date twist on the traditional die-cast manufacturing process, in which material is poured into a mold to make a part. In Tesla’s adaptation, its gigapress – made by specialty Italian engineering company IDRA – casts large aluminum parts for its cars. According to Tesla, the alloy used in the process has been specially developed by the company to bypass the heat treating typically used in such manufacturing to buttress the strength of the cast item.
The great advantage of manufacturing larger-than-average cast parts for autos is that the process can dramatically reduce the number of individual parts needed to produce a vehicle. IDRA claims that by using its machines, Tesla has cut costs as much as 40% in certain instances.
Mark Greenhouse, a U.K.-based operations management improvement consultant, put more specific numbers on Tesla’s gigapressing. According to him, the brand’s popular Model Y uses two castings which together replace 171 parts that were once pressed and cast on their own.
He says: “The supply chain is greatly reduced. No need to manage 171 different parts or their flow through the supply chain, check weld qualities, marshal trucks of supplies, store them, etc., As well as investment in machines or space, fewer robots means less investment, less maintenance and it sounds like a win/win.”
While Greenhouse is broadly optimistic about giga/megapresses specifically and effective alt-production methods generally, he points out they’re not exactly flawless: “There are risks with gigapress castings, mainly owing to tolerances and the different sizes of the part throughout the shape. The cast parts will cool at different rates owing to the cross-section size and proximity to parts that previously were made via another route. This may require heat treatments or straightening and re-work techniques to be applied post-casting.”
However, the super-sized press promise is enticing and other manufacturers have jumped on the bandwagon. General Motors recently adapted the process using megacasting to make six sand-casted aluminum pieces that form much of the ultra-luxury Celestiq BEV sedan’s body.
Another technology that promises to make life easier and cheaper for carmakers is 3D printing, known also as additive manufacturing. Such processes have been around for years now but the increasing scale of 3D printers gives automakers more scope to design the components they need. Turnaround is faster than it’s ever been, which can help greatly in potentially time-crunch situations like prototyping.
As with many aspects of today’s vehicle production, it’s too soon to tell which alternative production method or methods will come to the fore. At the moment, given the various niches being contested by specialty automakers, it seems there might be room for quite a few of them to at least be sustainable, if not dominant.
BEVs and other non-ICE models already have a crucial advantage that can be enhanced with efficient new production processes. Research analyst Wasif Jamal of consultancy Market Research Future says these vehicles “have very few parts as compared to the traditional car. Thereby, they require less time to assemble since they don’t have multi-speed transmissions, radiators, fuel injectors, gas tanks, valve trains or exhaust systems, to name just a few different components. It is estimated that while conventional drivetrains have as many as 2,000 parts, electric drivetrains can have fewer than 20.”
About the Author(s)
You May Also Like